As the bicycle industry is not as mature as the sailing industry in technology as in aviation industry, most companies spend less on development and research than on sales, so if the processing factory wants to sell materials to the bicycle manufacturers, it must do some responsibility for the research. For 100 years, the bicycle industry has been using steel as its material, and there is little need for improvement. Therefore, only a few engineers are engaged in research. Generally speaking, steel bicycle pipe processing plants know much more about how to produce a durable bicycle frame than frame manufacturers. Titanium tube used in bicycle and wheelchair frame was formed in the mid-1980s. Titanium application develops very fast, but as these small markets begin to heat up, the application process of titanium in the world slows down. As more and more cyclists begin to understand the benefits of titanium, they feel shy. TI-3AL-2.5V frame made of aviation quality pipes costs between $1600 and $3,500 each. The whole bicycle sells from $2,400 to $6,000. In the past four years, industrial pure titanium pipes and non-aviation TI-3AL-2.5V (transportation) Motion-grade) Titanium alloy frames are very popular. Some sports-grade titanium frames retail at a minimum price of $1,000 per pair and the whole bicycle at a minimum price of $1,700. In 1985, the purchasing power of titanium for frame was zero. In 1990, the purchasing power was about $1.5 million. By the end of 1995, the purchasing power was about $5 million.
Bicycle parts refer to crankshaft locators, pedals, handlebars connected to the frame. Titanium parts industry develops faster than TI-3AL-2.5V frame industry. Most of the parts are produced by Ti-6AI-4V, and most of the parts are processed by Ti-6A1-4V. The purchasing power of Ti-6A1-4V parts is only 1/3, 19,5 V of TI-3AL-2.5V frame. About 10 tons in 1997. Foundry parts can be SB is becoming more and more common, but this development may be slower than machine-added parts. Titanium suppliers are starting to provide cheap materials to titanium parts manufacturers. Most of these low-cost bicycle-grade materials are actually obsolete aviation materials. Compact, rigid and light weight are the general requirements for driving specifications of bicycles. Titanium is often not the best material, while forged and cast aluminium are more popular. If the price of Titanium Metal Matrix Composites (MMCs) falls, it may become an alternative to the current market for some aluminium applications. The material requirements of the frame are simple, but the driving characteristics are particularly critical, which complicates the selection of materials in some aspects. Most transport vehicles, structural elements and internal facilities and operating elements are separated. Until recently, all bicycle frames require structural integrity and mounting functions. There is no titanium alloy specially designed for bicycles. Only some materials have been improved for bicycles. Most people consider the cost reduction. The main problem of accepting titanium components is rigidity rather than cost. Ti-3Al-2.5V is the most commonly used titanium alloy for bicycles. Although it is developed for aircraft hydraulic system, it has formability and corrosion resistance. High fatigue strength to weight ratio and good elongation make Ti-3Al-2.5V conform to bicycle market performance standards. Compared with other titanium alloys, the greatest advantage of Ti-3Al-2.5V is its easy yield strength and tube forming, but its disadvantage is its poor price and modulus to density ratio. It is not easy to make Ti-3Al-2.5V extrusion as the dominant position of frame materials. Ti-6AI-4V also has some attraction. Its modulus and strength are higher than Ti-3Al-2.5V, but it is difficult to process small diameter pipes like bicycle frames. Ti-15V-3Al-6Cr-4Mo-4Zr is also easy to form, but its high density and low modulus offset its advantage of increasing strength.
If the titanium industry is interested in developing the titanium alloy sporting goods industry, including bicycles and wheelchairs, it should not only publicize the producers, but also the end-users of the products. After the failure of the titanium frame in the 1970s, although the excellent performance of the Ti-3A1-2.5V pipe has improved the reputation of titanium, it is vulnerable to the current progress. The threat of inexpensive industrial pure titanium frames entering the market, together with the titanium frames produced by some small companies, which do not have the knowledge and resources necessary to create successful titanium products, will affect the reputation of titanium in the bicycle industry and other consumer goods. This problem has been encountered in the sailing industry several years ago. Titanium has lost its reputation in the high-tech sailing market and is still prohibited from being used on racing sailing boats by the relevant authorities. Such problems can be avoided entirely through publicity.
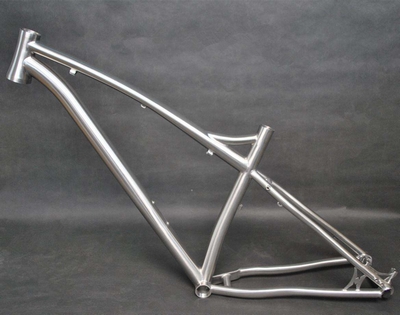
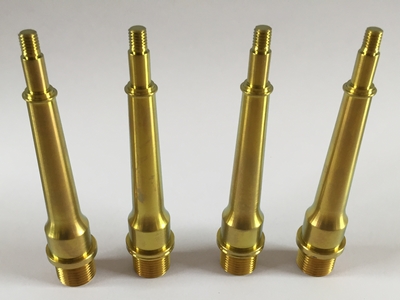
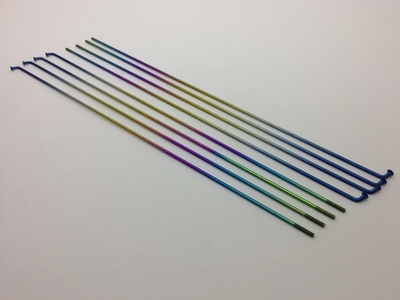